Efficiency of pumps is important in industrial applications. These types of pumps are designed to convert most of the input energy into delivery capacity hence cutting costs and enhancing performance in return. Therefore, gear pump versus lobe pump comparison becomes necessary for any industry seeking for best fit solutions. Right selection ensures accurate pressure control as well as gentle treatment of fluids while passing through them. Professionals should know how each one works differently efficient levels maintenance requirements and where they can be applied appropriately.
Understanding Gear Pumps
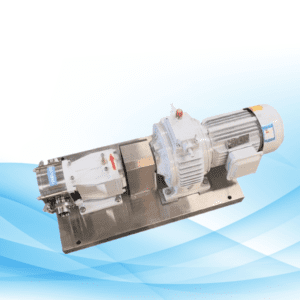
Definition and Basic Characteristics
These pumps are also known as Gerotor ones which use an internal gear with external gears having special geometry so that two components come into contact closely but do not touch each other at all points simultaneously thus achieving higher compactness along with better performance than any other type may offer alone or in combination thereof . They can meter precisely liquids or viscous materials due to a perfect meshing between their gears resulting definite volume per each turn made by them.
How Gear Pumps Work
Fluids are transferred by gear pumps using rotating cogs or gears; this creates liquid seal around the rotating element against pump casing thereby causing suction at its entrance point . As soon as fluid gets inside it wraps around cavities formed by teeth on opposite sides while being carried mechanically towards discharge side through these same teeth regions which produce smooth uniform flow rate directly proportional to number turns made per unit time.
Types of Gear Pumps (External vs. Internal)
There exist two main categories namely external as well internal .
- External Gear Pumps: This type consists mainly of two identical gears that interlock each other supported by separate shafts . It has ability to withstand relatively higher pressures up-to 7500psi because shaft support is more rigid due closer tolerances maintained during manufacture process.
- Internal Gear Pumps: Has one gear rotating within another with both having different sizes but they still mesh together . Such pumps are good at sucking in fluids since their suction capability is high; especially those of high viscosity which may easily break down when subjected to shear forces such as these ones generate.
Advantages of Gear Pumps
High Pressure Handling
Gear pumps have ability to create very high pressures making them suitable for applications requiring accurate pressure control. They can be used up to 7500psi where necessary.
Compact Design
These types of pumps are relatively small in size because there few moving parts involved; this therefore makes them more reliable and easy to fit into different systems without any problem. Their compactness also allows installation where space limited or not available altogether.
Disadvantages of Gear Pumps
Noise Levels
Compared with other pump technologies, gear pumps tend produce higher levels of noise . The intermeshing gears while rotating cause mechanical sound that might become disturbing especially if used close proximity quiet areas like residential zones during night hours.
Wear and Tear
With prolonged usage, gear pump’s gears usually experience wear out hence leading maintenance difficulties. Sometimes it becomes hard perform servicing on these machines since one has disassemble everything apart which takes much time as well energy; additionally frequent checkups should done maintain highest performance level possible by such mechanisms.
Understanding Lobe Pumps
Definition and Basic Characteristics
Rotary lobe or simply lobe pumps employ two or more lobes that rotate within a casing creating sealed chambers through which fluid is moved from one side to another. They are designed handle highly viscous liquids like pastes sludge etc., hence can be used widely across many industries dealing with different kinds thick materials. A robust construction guarantees longevity reliability even under extreme working conditions so they don’t break down easily during heavy duty processes.
How Does a Lobe Pump Work
Inside the casing of lobe pumps, there are rotating lobes. When these lobes rotate, it forms a sequence of closed chambers that push the fluid from the inlet to the outlet. Moreover, this type of pump ensures gentle treatment for shear-sensitive fluids because its lobes do not touch each other while moving hence reducing any harm on product which makes them applicable in situations where delicate liquid transfer is required.
Types of Lobe Pumps
There are several designs available for lobe pumps to cater for different industrial needs. The main categories include:
- Single-Lobe Pumps: These pumps use only one lobe in order to move liquids around. They work best with low-viscosity fluids.
- Multi-lobe Pumps: This type has more than two lobes thus increasing efficiency and capability of handling different types of liquids including those with larger particles or higher viscosities.
Advantages of Lobe Pumps
Safe Handling Of Fluids
The fact that they handle fluids gently makes them perfect for applications involving materials which are sensitive to shear forces. Besides, non-contacting nature between their lobes minimizes chances of damaging fragile items during pumping process such as foodstuffs, drugs among others used in cosmetic industry.
Versatility In Applications
Lobepumps can be employed across various sectors due to their ability to deal with wide range fluid properties. Such pumps have capability of managing high-viscosity fluids, slurries as well as those having solid particles suspended within them without causing any harm thereby making it suitable for many industries.
Disadvantages Of Lobe Pumps
Limited Pressure Range
Comparatively speaking gear pumps may operate at much higher pressures than lobe ones do since latter pump design gives priority over former to gentle fluid treatment at expense if necessary precise pressure control needed by some applications.
Bigger Size Requirement
Because robustness is part what makes uplobepump’s construction, this type generally occupies more space as compared with others. The need for extra room could be an issue during installation where there are size restrictions but usually larger sizes justify themselves through efficiency and longevity benefits.
Gear Pump Vs Lobe Pump: A Comparative Study
Efficiency In Different Applications
Viscous Fluids
High viscosity materials like paints oils resins etcetera can best handled by gear pumps which have ability to meter these substances accurately thus maintaining constant flow rates; furthermore such pumps remain efficient even when handling highly viscous fluids therefore being capable of meeting industry demands for stringent pressure control at all times.
Another good thing about lobepumps is that they perform effectively with such types of liquids too because its design allows it to operate on high speeds while reversing directions during conveying process which makes them perfect for industries involved in food processing pharmaceuticals where gentle fluid handling matters most.
Shear-Sensitive Fluids
In cases where shear sensitivity becomes a concern gear pump may not always be the right choice since intermeshing gears create mechanical stresses that can degrade delicate materials hence causing unwanted product alterations within applications dealing with sensitive substances.
This is why many people prefer using lobepumps over other kinds of pumps especially when transporting cosmetics or biotechnological products which require carefulness in transferring fluids without any damage being done onto them due to their fragility .
Energy Consumption
Power Requirements
Lobe pumps, though effective, are powerful due to their heavy-duty construction and increased flow rates. The added power guarantees that the system can work with viscous fluids and those containing particles without compromising its efficiency. The variety of fluids that can be handled using lobe pumps justifies their power usage effectiveness.
Operational Costs
Gear pumps have low operational costs because they are simple in design and require less maintenance. This means that gear pumps are easy to maintain which saves a lot of money in the long run because they do not need frequent repairs or replacements. For this reason, gear pumps are recommended for industries looking for cost-effective solutions.
Despite higher initial power requirements, lobe pumps have competitive operational costs. This is attributed to their ease of maintenance as well as durability which reduces downtime thus saving on costs in the long term. Also, these types of pumps can operate for longer periods without servicing due to their ability to handle different fluids without clogging hence being considered valuable investments.
Maintenance and Durability
Maintenance Frequency
Gear pumps must undergo regular maintenance since gears wear out through contact with one another during operation. Thus there is need for periodic checks so that worn-out parts can be replaced thereby increasing how often gear pump should be maintained but it is simple because only few parts need attention.
Non-contact lobes make lobe pump easier to maintain compared to gear pump whereby there is contact between two intermeshing gears resulting into wear and tear after some time of use. This design also reduces frequency at which lubrication necessary thus reducing number times when greasing or oiling required by such machines like this type may be done over certain period instead continuously every day as would have been case if had been using another kind therefore making them more reliable than others in terms maintaining them always ready for work even when used continuously under harsh conditions where other kinds fail due frequent service required caused by continuous running dry further being preferred many industries.
Lifespan and Reliability
Gear pumps are reliable but may have a shorter lifespan because gears wear out due to mechanical friction. If they are regularly serviced then their life expectancy can be prolonged although this cannot go beyond certain limit set by nature of design itself which affects how long gear pump lasts before breaking down completely still it remains best device for applications that require exact pressure control when used appropriately within its limits.
Lobe pumps last longer than gear pumps since there is no physical contact between parts except during installation or dismantling which means less wearing off takes place hence increasing years lobe pump will serve without developing any problem provided used correctly so as not damage surfaces where lobes come into contact with each other in case reverses flow direction. This robustness ensures that even if abrasive substances pass through them frequently over extended periods none wears which could compromise performance levels under harsh environments like those found industrial settings dealing corrosive materials where durability must be given more emphasis together with reliability terms working continuously throughout entire process without stopping because broke down somewhere along line due being unable withstand effects caused by such chemicals on materials used their construction thereby making them ideal candidates for handling different types fluids across various industries.
Practical Considerations
Industry-Specific Applications
Food and Beverage Industry
Pumps used in the food industry should be able to maintain product quality while ensuring hygiene standards are met. Lobe pumps are most suitable for such purposes since they do not subject shear-sensitive fluids to strong mechanical forces during pumping. The gentle action of non-contact lobes also helps in preserving delicate dairy products, sauces, beverages etc., whose integrity might have been compromised by high levels of agitation caused by other types of machines designed this way especially drinks containing solids like juices mixed pulp pieces or particles suspended within liquid itself besides meeting sanitation requirements necessary for cleanability (CIP) after use has been completed as opposed another kind.
Gear pumps can also find application in the food sector where accurate measuring needed alongside having capacity handle high pressures involved during production process. External gear pumps, for example, have proven effective at handling oils and syrups with different viscosities among other ingredients used in food manufacturing processes. However, some food products may not be compatible with mechanical action imparted by gear pump due to their sensitivity towards shearing forces induced when passing through narrow gaps between rotating elements of such devices thereby causing undesirable effects on quality attributes like texture taste appearance etc.
Chemical Processing
Chemical processing requires pumps that can handle a wide range of fluids including those which are corrosive or highly viscous. Gear pumps come in handy here because they allow solvents to be pumped at very high pressures while maintaining accurate flow rates required for resins and various types of chemicals being processed within industries dealing with this kind activities among others also it should be noted that compactness design makes integration into complex systems easier than any other type would do so even if space limited still possible install them where needed most without much effort being put into modifications made necessary by larger sizes associated lobe pump applications all over world but not all places suit every size hence why gear pump choice preferred.
Lobe pumps are known for their ability to work with fluids containing particles as well as those having different viscosities in chemical processing plants where there is need handle abrasive materials or deal with aggressive substances that could easily corrode ordinary parts used such environments besides having reversible flow capabilities make them versatile enough adapt diverse processes involving such chemicals across industry
Analysis of Costs and Benefits
Initial cost
The simplicity of design and low number of parts in gear pumps leads to a lower initial investment. This affordability makes them suitable for enterprises that have limited budgets. Moreover, gear pumps are characterized by space-saving features which minimize installation charges.
On the other hand, lobe pumps may appear more expensive at first glance but they offer long-term benefits that outweigh their high upfront costs. These pumps have strong constructions capable of handling various fluids without wearing out easily. Such qualities increase reliability levels hence most industries find it worth making an initial investment on them.
Saving over time
Gear pumps save money in the long term through lower operation fees as well as less maintenance requirements; this is because they have compact size and high energy efficiency. In addition to consuming less power due to good transferability of power which results from their small sizes i.e., low pulsation rates during metering process can be achieved using minimum amounts of energy possible thus lowering costs over years. It also helps if these machines receive regular servicing since it extends their lifespan while maintaining optimal performance always.
Lobe pumps still manage to deliver considerable savings even though there might be increased electric power demand during start up phases when compared against other types such as screw or centrifugal ones. The reason behind this is that easy care gives way for reduced downtimes together with affordable repairs considering robust nature besides being able to handle different liquids without frequent replacements for parts leading into longer life span hence more savings especially for those seeking reliable industrial pumping solutions.
Each category has its own strengths which become clear after comparing gear pump versus lobe pump systems. For instance, gear units work best under conditions where pressure levels are higher while also being capable of offering energy efficient services during low pulsation metering processes. However, lobe type devices excel at gently treating shear sensitive fluids as well as managing wide range viscosity variations among others things too numerous to mention here but all aimed towards ensuring that customers get value for their money when purchasing these machines. Therefore, it is important to determine the specific needs and applications before making a choice between different pumps. Gear models are recommended where accurate control of pressure is required at minimum cost while lobe units perform better in situations involving delicate transfer fluids with high efficiency . They can also be used in places where there might be need to employ both methods so as achieve desired goals faster than using one method alone.
When deciding which system would work best efficiency, maintenance and suitability should be considered in order to come up with the most appropriate solution for a given application or industry.