It is important that you choose the right oil transfer pump as this will guarantee efficiency and save you money. Different pumps are made for different oils and situations. Selecting the right pump can significantly affect energy consumption and overall performance especially when dealing with varying fluid viscosities where high resistance requires more power due to increased viscosity. Understanding these factors will enable you to make informed decisions that are efficient in terms of both time and cost.
What are Oil Transfer Pumps?
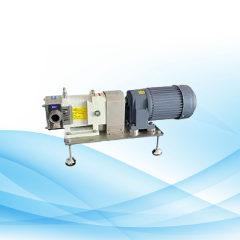
Types of Oil Transfer Pumps
Gear Pumps
Oil in gear pumps is moved from one point to another by rotating gears. These pumps work well in high-pressure areas because they create a vacuum as they rotate which draws oil into their chambers. Gear pumps can handle oils with different thicknesses but need regular maintenance so that they do not fail to perform their duties.
Diaphragm Pumps
Diaphragm pumps use diaphragms, valves, and chambers to push oil through them. They also have fewer moving parts thus durability is enhanced since there is low wearing out during operation compared to piston or rotary vane varieties. However, this may cause slight variations in fluid output throughout its operating cycle making it suitable for transferring oil across many industries.
Piston Pumps
A piston moves up and down inside a cylinder thereby creating a pressure difference on either side hence sucking or pushing oil from one point to another depending on its usage (single-acting or double-acting). These produce very high pressures hence best suited for thick oils like those used in hydraulic systems, lubrication among others where accurate flow control is required. Nevertheless, frequent cleaning should be done lest premature failure occurs due to dust accumulation because most automotive industries employ such machines.
Rotary Vane Pumps
Vanes attached off-center to a drive shaft-mounted rotor revolve within size-changing chambers as the rotor spins round. Rotary vane pumps use oil for lubricating parts and making tight seals so that no air gets into it while running which may affect its ability to achieve deep vacuum compared to diaphragm pumps. They are relatively cheaper than most pumps though they require regular maintenance. These are multipurpose machines suitable for various applications.
How Oil Transfer Pumps Work
Basic Mechanisms
Oil transfer pumps of different types work mechanically in various ways depending on their design features. For instance, gear pumps rotate gears to create a vacuum while diaphragm ones have diaphragms and valves within chambers where oil passes through during the pumping process. Piston pumps displace fluid by reciprocating pistons moving back and forth inside cylinders thus creating high pressures needed for pushing through thick viscous fluids such as heavy fuel oils or bitumen used in road construction. Rotary Vane pumps use vanes mounted off-center to rotate within changing-sized chambers for efficient oil movement.
Crucial Parts
The parts and components of oil transfer pumps are comprised of several elements each with its own specific function aimed at ensuring efficiency during operation. Gear pumps have rotating gears that create a vacuum which sucks oil into the chamber. Valves, diaphragms, and chambers through which oil flows due to pressure differences caused by the movement of valves connected with diaphragms make up diaphragm pumps. Piston types have pistons enclosed in cylinders that move up and down thereby creating necessary pressures for propelling fluids from one place to another depending on the application. Rotary vane pump assemblies consist among other things of vanes mounted off-center on a drive shaft-mounted rotor that rotates inside changing-sized chambers.
Considerations When Choosing an Oil Transfer Pump
Type of Oil
Viscosity
Viscosity affects pump performance significantly hence higher torque should be considered when dealing with high-viscosity oils. Positive displacement pumps work well with viscous fluids because they possess low slip as well as high volumetric efficiency. Accurate viscosity corrections must therefore be known for proper sizing of pumps.
Temperature
Variations in temperature affect viscosity whereby heat reduces thickness making it easy to pump hence less energy required while cold increases density thus demanding more power for transfer; therefore select a pump that can operate within the expected operational temperature range to achieve the best results.
Flow Rate Requirements
Rate of Flow Calculation
To determine the volume of oil that needs to be transported over a given period, it is important to accurately calculate the flow rate using the formula:
[Flow Rate = Volume / Time]
This ensures precise fulfillment of particular operational requirements by the chosen pump.
Pump Capacity Matching
Match the capacity rating of the pump with the calculated flow rate; overestimation leads to inefficiency and higher cost whereas underestimation results in poor performance hence ensure that the rated capacity matches the required flow rate for maximum efficiency.
Power Source
Electric Pumps
Electrically driven machines may cause the ignition of flammable gases or dust clouds leading to explosions thus pneumatic pumps are mostly used in hazardous environments. Electric pumps have constant flow rates and are user-friendly; these types require power which should be readily available hence applicable where there is electricity. They can run continuously without failing therefore they work reliably during operation especially when large quantities are supposed to be pumped over long distances for industrial use.
Manual Pumps
Manual pumps are suitable for small-scale operations due to their low cost. These pumps do not need electrical energy so they can work even in areas where there is no electricity at all. Moreover, being portable and rarely used or only during emergencies makes them easy to maintain.
Pneumatic Pumps
Compressed air-driven machines may cause the ignition of flammable gases or dust clouds leading to explosions hence pneumatic pumps are commonly used in hazardous environments. It requires a continuous supply of compressed air but once it starts working, it remains robust and reliable throughout operation time.
Environmental Conditions
Indoor vs Outdoor Use
During selection of an oil transfer pump, one should consider whether it will be installed indoors or outdoors. Indoor installations take place under controlled conditions with minimal exposure risks while outdoor installations have to withstand harsh weather conditions such as heavy rains, strong winds, and temperature changes. Weatherproofing against moisture ingress can be achieved by using materials that resist corrosion.
Temperature Extremes
The ability of the pump to work is affected by extreme temperatures. Pumping becomes easier for oil at a higher temperature because its viscosity decreases but increases with lower temperature which means that more energy must be supplied into it. The best pumps should be selected that can operate efficiently over the expected ranges of temperatures since they usually have built-in controls for temperature regulation.
Material Compatibility
Pump Materials
The type of oil being pumped determines the material from which a pump should be made. Some oils may not go well with certain materials leading to corrosion, abrasion, or failure altogether. Rust resistance is good in stainless steel but not in aggressive environments while cast iron provides strength but may be attacked by corrosive substances. Plastics are therefore more suitable for offshore applications due to their chemical inertness and lightness.
Oil Types
Different types of oils have different properties which affect how they interact with materials used in constructing pumps. Mineral oils corrode less than synthetic ones and can work with many other substances. Based on their chemical nature, bio-based lubricants require careful assessment when it comes to selecting pump compatible materials.
Positioning and Foundation
Installation Location
Where you put your pump during installation will greatly determine its efficiency. Proper planning should involve finding an appropriate place within which mounting an oil transfer pump can lead to minimum losses as well as easy accessibility for regular checks and maintenance practices.
Support Structure
For the smooth operation of any oil transfer pump, there must be a strong support structure beneath it. The machine’s weight has to rest on something solid while vibrations produced during its functioning are absorbed by this same object. Failure could result if misalignment occurs due to lack of adequate support leading to increased wear. Concrete pads or steel frames provide the stability required here.
Practical Examples and Comparisons
Case Study 1: Industrial Use
Requirements
Strong pumps made from robust materials are needed in industries where heavy-duty tasks need to be performed continuously. The selected pumps should be able to handle oils of different viscosities non-stop and also have resistance against severe chemicals as well as wide ranges of temperatures.
Chosen Pump and Rationale
Gear pumps are most suitable for industrial purposes following their ability to work under high-pressure conditions more effectively through the utilization of rotating gears which draw in oil by creating a vacuum effect. Stainless steel among others is used because it has good corrosion resistance properties hence being an ideal material for making gear pumps.
Case Study 2: Automotive Use
Requirements
Pumps designed specifically for medium-high viscosity grade lubricants are required in the automotive sector. The facility should allow easy regulation of flow rates especially when dealing with delicate tasks such as changing oil or greasing parts. Durability and ease of maintenance cannot be ignored within workshop environment settings.
Chosen Pump and Rationale
Piston pumps can work best for automotive applications due to their capability of generating large amounts of pressure needed to distribute oils with varying thicknesses. These types of pumps perform reliably in workshops where heavy-duty work done using thick oils is involved.
Case Study 3: Agricultural Use
Requirements
Agricultural pumps must operate under dusty conditions that experience frequent fluctuations in temperature. Being aware of this fact will help you choose a portable one since farmers move from place to place quite often during their activities. Bio-based oils should also be considered when selecting those capable of handling them.
Selected Pump and Reasoning
Farmers usually choose diaphragm pumps on their farms because they are made up of a simple structure, contain few moving parts, and thus wear out less. Lightweight allows moving them easily at work sites while being dependable enough for any farming operation.
Conclusion
There are many things that must be taken into account when selecting an oil transfer pump. It is important to know what types exist, how each works, and where you will use it so as not to make the wrong choice. By choosing one according to specifics ensures the least cost with the highest efficiency, also seeking advice from professionals or looking through more information can help a lot. These things need proper care otherwise they won’t last long or give desired results – maintain them well if you want your pumps to serve longer!