Introduction to Rotary Lobe Pumps
Selecting an appropriate rotary pump, for example, a lobe pump, can be one of the most critical factors in the production stream where liquid movement is involved. They have proved to maintain reliability, manage viscous material in a gentle manner, and are multifunctional. This guide provides every relevant detail about rotary lobe pumps, including their operation, uses, advantages, and the latest technologies that could shape how rotary lobe pumps are viewed in the future.
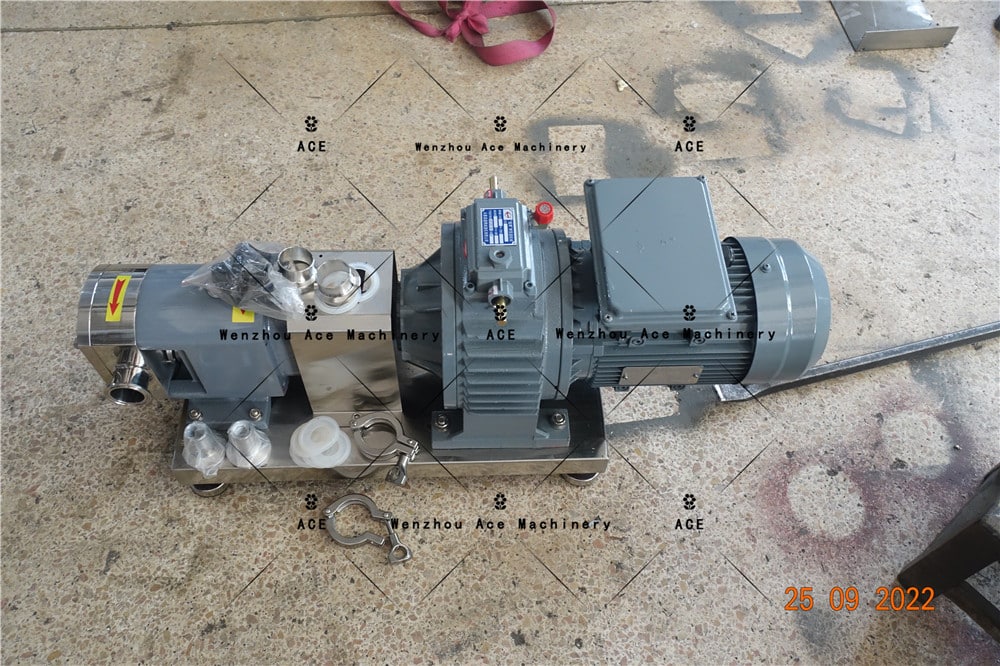
How a Rotary Lobe Pump Works and Its Applications
This type of rotary lobe pump is a positive displacement pump widely used in the positive rotary pumps industry where careful and precise fluid movement is required. Unlike centrifugal pumps that rely on velocity for liquid movement, rotary lobe pumps use rotating lobes to capture and pull liquid to the pump’s exit. This method of fluid transfer is ideal for viscous and shear-sensitive materials, making it suitable for sectors like food and beverage, pharmaceuticals, and wastewater treatment.
Rotary lobe pumps are preferred for pumping various liquids, including highly viscous ones like creams, syrups, and slurries. Since the lobe design allows for handling solid particles in suspension, they are used in applications where the fluid’s integrity must be preserved without damaging the material.
How Does a Rotary Lobe Pump Operate?
Rotary lobe pumps have a simple yet efficient mechanism. The pump contains two or more lobes that move in opposite directions. As the lobes rotate, cavities form at the pump’s inlet, allowing fluid to fill the chamber. As the lobes continue to rotate, the outlet-side cavities reduce in volume, expelling the fluid from the pump.
One crucial aspect of rotary lobe pumps is that the lobes do not contact each other. This design minimizes wear and tear, resulting in long service life and reduced maintenance. Additionally, this feature enables rotary lobe pumps to handle materials with significant viscosity variations, such as water and thick, pasty substances.
Important Parts of a Rotary Lobe Pump
Understanding a rotary lobe pump’s operation also requires understanding its components, which include:
- Lobes: Rotating parts that form cavities to transfer liquid.
- Pump Casing: The perimeter housing the lobes and fluid displacement.
- Seals and Bearings: Mechanisms that prevent leakage and support lobe placement.
- Shafts: Members transmitting lobe motion to the motor or drive.
- Timing Gears: Components ensuring lobes rotate in sync and without contact.
Benefits of Employing Rotary Lobe Pumps
Rotary lobe pumps offer several benefits that make them a preferred choice across various sectors:
- Gentle Fluid Handling: These pumps are gentle and low-shear, suitable for high-value and sensitive materials like food and pharmaceuticals.
- Versatility: They handle fluids with a wide viscosity range, including fluids with solid particles.
- Durability: The non-contact design of the lobes reduces wear, making these pumps reliable with proper maintenance.
- Reversibility: They offer flexibility across different stages of processes, despite the inability to reverse operations.
- Low Maintenance: The design minimizes the need for frequent maintenance.
- Sanitary Design: Their strict hygiene standards allow for use in cleanroom applications.
Applications of Rotary Lobe Pumps
Rotary lobe pumps have broad applications across multiple industries:
1. Food and Beverage Industry
These pumps are ideal for handling delicate food products like yogurt, honey, sauces, and fruit purees, thanks to their gentle action.
2. Pharmaceuticals
Rotary lobe pumps are recommended for transferring creams, gels, and other medicinal products hygienically and in precise quantities.
3. Wastewater Treatment
These pumps are suitable for pumping sludge, slurry, and viscous materials during sewage and water treatment operations.
4. Chemical Industry
They are widely used to transfer caustic liquids and dangerous materials in chemical industries due to their durability and chemical resistance.
5. Cosmetics
Rotary lobe pumps handle viscous cosmetic materials like lotions, creams, and gels effectively without causing damage to the product.
Rotary Lobe Pumps vs. Other Types of Pumps
When selecting a pump, common comparisons are made with other types:
- Centrifugal Pumps: Efficient for high flow rates but inefficient with high viscosity and shear-sensitive fluids.
- Diaphragm Pumps: Accurate metering but often more complex, requiring more maintenance.
- Gear Pumps: Similar to rotary lobe pumps, but better suited for compact, steady applications.
Varieties of Rotary Lobe Pumps
Rotary lobe pumps are subdivided based on the number and configuration of lobes:
- Bi-Wing Lobe Pumps: Ideal for handling larger solids.
- Tri-Lobe Pumps: Reduce pulsation flow, suitable for food and pharmaceutical applications.
- Multi-Lobe Pumps: Offer the smoothest operation for high-precision applications.
Materials Used in Rotary Lobe Pumps
The performance, lifespan, and application of a rotary lobe pump are influenced by the materials used in its construction, including:
- Stainless Steel: Common in food and pharmaceutical use for its cleanliness and non-corrosive properties.
- Elastomers: Used for seals and gaskets to ensure leak tightness and compatibility with various fluids.
- Alloys: Resistant to harsh chemicals, commonly used in the chemical industry.
How to Select the Right Rotary Lobe Pump
Several factors should be considered when selecting a rotary lobe pump:
- Fluid Characteristics: Viscosity, temperature, and the presence of solids affect pump selection.
- Flow Rate: The required flow rate will determine the pump size and type.
- Operating Conditions: Pressure and temperature conditions must be evaluated.
- Material Compatibility: Ensure pump materials are compatible with the fluid to prevent corrosion or wear.
Maintenance and Troubleshooting of Rotary Lobe Pumps
Regular maintenance is essential to ensure the durability and consistent functionality of rotary lobe pumps:
- Seal Inspection: Periodically assess seals to prevent leaks and contamination.
- Bearing Lubrication: Regular lubrication avoids breakdowns.
- Cleaning: For hygienic applications, thorough cleaning is necessary to prevent contamination.
- Troubleshooting: Address issues like reduced flow, noise, or leakage to prevent damage or production loss.
Rotary Lobe Pumps in Hygiene-Critical Processes
Rotary lobe pumps have significant advantages in hygienic applications, such as in the food, beverage, and pharmaceutical industries. Their design facilitates cleaning and sterilization, minimizing microbial contamination and meeting strict FDA and EHEDG standards.
Current Developments and Prospects for Rotary Lobe Pumps
Significant progress is being made in the rotary lobe pump market, focusing on improving performance, reducing energy consumption, and enhancing material properties:
- Energy Efficiency: New designs reduce energy consumption in large-scale industries.
- IoT Integration: IoT and automation features allow easy monitoring and predictive maintenance.
- New Materials: Innovative materials like corrosion-resistant alloys and wear-resistant plastics enhance pump durability.
Popular Queries Relating to Rotary Lobe Pumps
What is the lifespan of a rotary lobe pump?
With proper maintenance, rotary lobe pumps can last several years, with some models exceeding 10 years.
Are rotary lobe pumps able to pump solids?
Yes, they are particularly suited for pumping fluids with suspended solids, such as in food processing and wastewater treatment.
What is the typical viscosity range for a rotary lobe pump?
Rotary lobe pumps can handle fluids ranging from water-like viscosity to thick pastes up to 1,000,