A Brief Introduction to Rotary Pumps
Rotary pumps are mechanical devices that are used for the transfer of fluids, in which rotational energy is used to move either a liquid or gas from one part of the system to a different part. Unlike other types of pumps that tend to be activated by pressure differences or mechanical displacement activity, the rotation pump works by means of constant rotation of its internal structural components. Its internecine construction system enables it to accommodate a number of fluids such as thick gasses, making it useful in a range of industrial applications. Their dependability and effectiveness are some of the contributing factors to the wide range of usage of the pumps in oil, gas, chemicals, and even most homes where appliances are used frequently. It cannot be denied that rotary pumps form an important part of most industries. They are often used as the main components in fluid transfer facilities, helping to maintain the desired flow and pressure within acceptable limits for effective operations. As the industry progresses, the need for rotary pumps as an optimum solution to fluid management has not decreased. It remains high, and very much so because of the way industries grow. The last section of this chapter looks at rotary pumps.
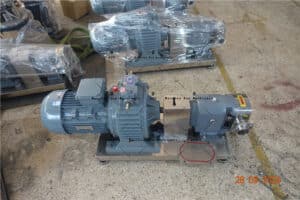
Defining and Isolating Issues
Rotating pumps definitions and basic explanations of terms: rotary pumps are positive displacement pumps which are used for the transport of liquid or fluid by forming an enclosing volume containing a certain amount of liquid and moving it into the discharge pipe. It must be noted that these pumps operate on the basic axiom of their parts rotating around the leads. This rotation is responsible for creating a difference in pressure that moves fluids.
Function Of Rotary Pumps
It is almost obvious that the operation of rotary pumps is simple. A fluid containing chamber is created when the rotor of the pump rotates, which makes it possible to pull in fluid from the inlet side. This fluid which has been confined is then carried to the discharge side as the rotor of the pump moves on further. This design guarantees a constant outflow of fluid and therefore ideal for processes that require fixed outputs.
Main Elements
Key components of rotary pumps are related to rotor, stator, inlet and outlet ports, and seals. While the rotor helps in inducing motion to the fluid, the stator mainly serves as a support. The inlet and outlet ports guide the flow of fluid in and out of the system, while seals are features towards preventing the leakage of fluids for effective functioning.
Evolution Over Time
The history of a rotary pump can be traced back to the old days, and some rotary pumps date back to Ancient Egypt. They originated with the first rotary pumps. Even so, these pumps were very primitive and depended on simple common mechanical concepts. In the course of years, the improvement concerning materials as well as engineering made people come up with more intricate designs. Significant areas of progress include the second industrial revolution through to the introduction of gear and vane pumps towards the 19th century. These improvements increased the operating parameters and the efficiency of rotary pumps, which contributed to their fast uptake in several sectors.
Rotary Pump Types
Gear Pumps
Among the most popular types of rotary pumps are the gear pumps, which have interlocked rotating gears that transfer fluid within the pump.
Internal Gear Pumps
Internal gear pumps can be described as a gear inside another larger gear where fluids are pumped. The efficiency of this unit is quite remarkable and it best suits moving thick fluids.
External Gear Pumps
External gear pumps contain 2 meshing, somewhat counter rotating gears. They induce fluid into the pump and are suitable for fluids of lower viscosity and also when high volumes of fluids are demanded.
Vane Pumps
The inlet of a vane pump is usually fitted with sliding vanes that extend out and form a cavity inside the pump as the rotor rotates, creating suction to pull in fluids.
Sliding Vane Pumps
These special pumps have sliding vanes that can be used for low viscosity fluids, but which experience changing flows. Their adjustable vanes then allow them to be effective when the fluid’s viscosity changes.
Flexible Vane Pumps
Flexible vane pumps utilize the flexible vanes that are able to accommodate the fluid narrow viscosity range, which makes them applicable in both abrasive and non-abrasive applications.
Screw Pumps
Rather than using a packing, one or more screws are utilized to transport the fluid through the pump.
Single Screw Pumps
These pumps utilize a single helical screw that moves the fluid through the cylindrical pot. They are chiefly used where fluids of very high viscosity are handled.
Twin Screw Pumps
Twin screw pumps are configured such that the two screws cut into each other and hence fluid is conveyed by these two screws. They are preferred because they convey different types of fluids with little pulsation.
Functions and Applications
Industrial Uses
Rotary pumps are quite important in various industries.
Oil and Gas Industry
In oil and gas industries, the transport of crude oil and other hydrocarbons is facilitated by rotary pumps. There, precision in oscillator pumping is crucial in the movement of viscous fluids.
Chemical Processing
As for chemical processing, rotary pumps are used to pump hazardous and corrosive liquids. The strength as well as dependability are important in reducing delays and increasing safety.
Domains of Daily Use
Rotary pumps are also used in normal implements.
Mr and Mrs Motors
In automobiles, rotating pumps are usually incorporated in fuel injectors to ensure a steady supply of fuel into the engine for effective working.
General Use Appliances
Various general use appliances that include washing machines and dishwashers employ the use of rotary pumps to control the flow of water, portraying their uses even in mundane activities.
Advantages and Disadvantages
Benefits of Rotary Pumps
Many benefits come along with the use of rotary pumps.
Efficiency and Reliability
It is inherent knowledge to understand that these pumps are efficient and reliable in performance, being able to withstand strenuous operation for prolonged periods of time. Their use is further enhanced by the fact that they are capable of handling an extensive range of fluids.
Versatility in Applications
Rotary pumps are not confined to one industry or one application, they are used for many applications for example handling viscous fluids, transferring corrosive chemicals and many others.
Potential Drawbacks
Nonetheless, there are some potential disadvantages.
Maintenance Requirements
It is standard practice to consider the maintenance of rotary pumps. This may involve changing seals and monitoring internal surfaces for wear.
Limitations in Specific Conditions
There are situations where rotary pumps do not perform well in high pressures or certain fluid types, and hence require careful selection in relation to application requirements.
Comparison with Other Pump Types
Rotary vs. Centrifugal Pumps
From the perspective of rotary pumps vis-a-vis centrifugal pumps, the capacities are utilized differently.