Rotary lobe pumps can perform at their best if they are subjected to constant maintenance. Maintenance has several benefits when done consistently. The life of the device is extended and its performance improved through maintenance. These machines have a longer lifespan because of the materials used in making them which are superior quality and they are also strong hence can work well even under tough conditions. They are also easy to maintain, operate continuously and offer flexibility too. Below are some tips for maintaining rotary lobe pumps:
Frequent Checking of Rotary Lobe Pumps
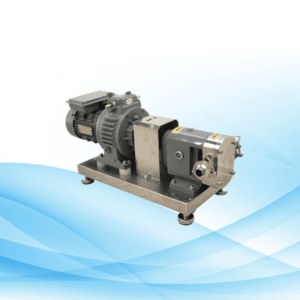
Regular examination plays an important role in ensuring that rotary lobe pumps last longer while still operating efficiently. By doing these checks, one is able to detect potential problems early enough so as not let them affect how well the pump works.
Visual Inspection
Check for Leaks
Once detected, leaks may signify severe internal failures within the rotary lobes itself; therefore it is essential that technicians inspect all seals, joints or connections where there could be any signs of fluid leaking out from such points because failure to do so might lead into more damages being incurred thus raising costs incurred during repairs.
Check for Worn out Parts
The functionality of a rotary lobe pump can be affected by wear and tear. Therefore during regular visual inspections, one should pay close attention on rotors or casing among other key areas so that any worn part does not go unnoticed since this will ensure timely replacement which is necessary for maintaining optimum performance levels.
Operational Inspection
Monitor Noise Levels
Uncommon noise levels usually indicate an underlying problem with the functioning of a rotary lobe pump. Technicians need to listen carefully for any strange sounds produced during operational hours as consistent monitoring helps in detecting misalignment issues or bearing failures etcetera.
Check Vibrations Regularly
A lot can go wrong if excess vibrations occur within this machine type; hence it becomes necessary always carrying out vibration checks on them to ensure that such pumps run smoothly without causing unnecessary damages elsewhere. Whenever there is an abnormal or too much shaking felt by hands while touching around its various parts then something has definitely gone awry somewhere along the line – take this as a sign that something needs attention now rather than later because failure to do so might lead into more severe damages being incurred thus raising costs during repairs.
Lubrication
For a rotary lobe pump to operate smoothly and last long, proper lubrication is needed. Regular greasing helps reduce friction which in return ensures better performance.
Types of Lubricants for Rotary Lobe Pumps
Best Lubricants
The choice of lubricant matters a lot; therefore people should go for synthetic types since they provide the longest life between oil changes which means these ones will offer better protection as well as performance over others. It is always good practice to follow what manufacturers recommend when it comes selecting suitable products for use with specific machines like those used in pumps.
Frequency of Lubrication
Observing correct lubrication frequency is important so that everything can work out just fine. For instance, check quench liquid or buffer fluid after every 200 hours of operation; inspect gear oil after each 500 running hours or at least quarterly if not sooner when heavy duty operations are involved while changing oil for continuous use should be done after every three thousand working hours minimum but if less were used then do it within three hundred hours instead.
Procedure for Greasing Properly
- Preparation: have all required tools and materials ready;
- Inspection: take note of current level & state;
- Draining: remove old grease from pump;
- Cleaning: ensure cleanliness around grease points;
- Refilling: add recommended amount up-to required level;
- Final Check: confirm no leaks and smooth running throughout system.
Common Mistakes Made During Lubrication
Using wrong greasing agents can cause harm; therefore avoid them. Do not pour too much neither little greases into various points. Cleanliness should be maintained so that contaminants do not find their way inside machines during such exercises. Regularly check gearbox oil levels then top up when necessary otherwise failure to do this might make parts wear out quickly leading to operational failures.
Cleaning
To keep rotary lobe pumps in good working condition for a long time, it is important to clean them regularly. Routine cleaning prevents contamination and build-up which may affect the efficiency of these devices.
Cleaning Processes
Internal Cleaning
The first step to internal cleaning is taking the rotary pump apart. Clean all surfaces by removing rotors and other parts. The reason for doing this is to eliminate any buildup which might affect its performance later on. Some designs are easier to clean than others and need sterilizing less frequently too, thus reducing chances of contaminating them further. In addition smoothness plus lack of dead spaces also helps prevent accumulation of residues.
How to do it:
- Disassemble Pump – Remove rotor blades and other internals.
- Clean Everything – Use appropriate agents for respective materials used in making different pieces.
- Look out for damages – Examine every part keenly checking for signs like wear or tear brought about by working conditions as well as poor handling during installation/ removal processes among other things.
- Re-assemble the machine back together ensuring all components fit properly and securely into their sockets or slots provided for such purposes within its structure thereby not allowing any air leakages whatsoever.
External Cleaning
External cleaning focuses mainly on outer surface areas around the lobes where dirt can easily accumulate over time if neglected altogether thus causing problems later on when least expected especially during critical operations’ moments like pumping abrasive fluids through thin clearances between impellers’ tips etcetera! Routine external cleaning therefore should never be underestimated at any given moment since failure may result into costly breakdowns besides affecting performance adversely too!
How to do it:
- Wipe All Surfaces Clean – Dampen some piece of cloth then wipe off everything gently until dry using another one after that if necessary so as not leave behind any moisture content thereon which could lead rusting/ corrosion eventually destroying delicate parts affected by these reactions; remember also avoid scratching painted areas with hard objects while carrying out this exercise since they easily get damaged even more than metallic ones when rubbed against rough surfaces repeatedly over time hence compromising appearance thereafter just wiping away dust particles accumulated over years leaving behind shiny new look everywhere instead!!
- Use Soft Brush For Stubborn Dirt – Sometimes dust particles might be stuck onto certain places due to their high electrostatic charge hence require a soft brush during the cleaning process however care must be taken not to scratch off paint jobs done during manufacture/ finishing touches applied afterwards otherwise it will have achieved nothing apart from making things worse off than they were before!
- Check for Corrosion or Mechanical Damages – Carefully inspect all external surfaces looking out for signs like rusting, pitting corrosion among others as well as physical distortions caused by mechanical forces such as abrasion rubbing against rough edges whereby necessary remedial action can be taken immediately before it’s too late thereby ensuring proper functionality throughout its lifespan though these may vary depending on materials used in manufacturing at the same time also considering operational environment which could determine the rate of deterioration experienced over specified period(s) hence should never neglected under any circumstance whatsoever!
- Dry The Whole Pump Thoroughly – Ensure that no moisture is left behind on any part of the pump
- Test: Start the pump to see if it is running and fix any problems.
These steps will help ensure a smooth replacement process and restore the pump’s functionality.
Ensure Proper Fit
It is important to ensure that new parts fit correctly. If parts are out of line, they can cause inefficiency or damage. Use alignment tools to check that components are positioned correctly. Look for spaces or misfits which may cause operational problems. Proper fit guarantees long life and efficient operation of rotary lobe pump.
Regular component replacement and proper fitting improve performance and extend the life of rotary lobe pumps. Following these guidelines will ensure reliable operation while minimizing downtime.
Alignment
The Significance of Good Alignment
Correct alignment plays a major role in the efficiency and durability of rotary lobe pumps. When it is not aligned properly, several things can go wrong with this vital equipment leading to inefficiency as well as unreliability.
Effects Of Misalignment
Various problems arise due to misalignment in rotary lobe pumps:
- Increased Wear And Tear: Uneven stress on parts that do not have evenness results in faster wearing out.
- Lower Efficiency: Disruption of smooth running throughout causes a reduction in overall efficiency realized by the pump.
- Higher Energy Consumption: Power demand goes high when operating a machine that has fallen out-of-line thereby increasing electricity bills.
- Possible Damage: Long periods under wrong position might cause severe internal breakdowns which may need expensive repairs for rectification in the future.
Alignment Tools
Some tools necessary for achieving proper alignment include:
- Dial Indicators: To measure rotating component exactness during alignment;
- Laser Alignment Systems: For accurate quick checks on alignments;
- Straight edges & feeler gauges: Used in checking flatness between two surfaces among other measurements required during aligning activities like spacing between objects etcetera.
The utilization of such devices ensures precise positioning thus improves performance together with service life span for these pumps.
Methods Of Aligning
Appropriate Methods for Aligning Rotary Lobe Pumps
It is crucial to follow the correct techniques of aligning rotary lobe pumps if they are to continue operating optimally. This will ensure accurate results while carrying out maintenance activities.
Step By Step Guide
- Preparation: Gather all necessary alignment tools and safety equipment.
- Initial Inspection: Look out for visible signs of misalignment or damage.
- Set Up Dial Indicators or Laser Systems: Place alignment tools as per manufacturer’s guidelines.
- Take Initial Alignment Measurement: Record initial alignment readings so as identify any deviations.
- Adjust Components: Make necessary adjustments for aligning components correctly.
- Recheck Alignment: Take another measurement in order to confirm accuracy of alignment.
- Secure Components: Tighten bolts and fasteners so as not lose achieved alignment during operations.
- Final Inspection: Carry out a final check to ascertain proper alignment has been achieved after all other steps have been followed through accordingly.
These steps will enable one achieve precise positioning thus reduce chances of experiencing operational challenges with such machines.
Common Problems And Solutions
During maintenance, there are some common problems associated with aligning these devices:
- Thermal Expansion: Changes in temperature can cause expansion or contraction of parts leading to misalignment; therefore materials having low coefficient thermal expansions should be used where applicable so that this effect is minimized.
- Vibration: Too much shaking can interfere with good alignment hence it is important to regularly inspect sources which could be causing vibrations and take necessary corrective measures before they affect the entire system’s performance negatively;
- Wear And Tear: Wearing off worn-out areas may result into wrong positioning hence regular checks should be done followed by replacing them with new ones for proper fitting always maintained throughout their service life span otherwise efficiency levels would drop significantly thereby affecting reliability too adversely over time if left unattended to promptly when noticed first during operation of these machines;
Addressing such issues in a timely manner will allow for smooth operations of the rotary lobe pump.
Temperature Measurement
Right Temperatures for Positive Displacement Pumps
Suggested Range of Temperature
Positive displacement pumps work most effectively when their temperature is maintained within particular limits. Generally, producers recommend an operating window of 50°F to 140°F (10°C to 60°C). This guarantees the best efficiency and durability. Monitoring the pump’s heat regularly helps keep it within these limits.
Effects from Overheating
Rotary lobe pumps can be severely affected by overheating. High temperatures cause thermal expansion which in turn leads to misalignment and increased wearing off. Besides, too much heat degrades lubricants more quickly thereby reducing their efficacy. Extended exposure to elevated temperatures can damage seals permanently as well as rotors and other vital parts of the machine. Such problems are averted by monitoring and regulating the temperature so that safe operation is assured.
Methods for Controlling Temperature
Ways of Cooling Down
Cooling down is important in maintaining optimum temperature for rotary lobe pumps. For moderate control overheat systems, there are air-cooled systems which use fans to let out heat while water-cooled provides better cooling effect for high-temperature applications. Installing a cooling system designed around operational conditions improves performance and prevents overheating.
Insulating Techniques
These techniques help in keeping constant temperatures within rotary lobes pumps. Thermal insulation materials like fiberglass or mineral wool are used to minimize heat transfer. Application of insulating material on pump casing together with piping reduces fluctuations in temperature. Appropriate insulation ensures that pump functions within recommended temp range hence improving efficiency and prolonging its life span.
It is necessary to regularly monitor temperatures so as ensure reliable service from positive displacement machines. Cooling efficiency should be enhanced by implementing good methods of insulation thus preventing them from getting heated up excessively.
Pressure Measurement
Significance of Pressure Regulation
Inspection: Check PRVs and regulators for wear or damage regularly. Replace any faulty parts to ensure they work.
Cleaning: Clean pressure control devices by removing any build-up that could affect their performance. Use proper cleaning agents and follow safety rules.
Testing: Carry out tests on pressure control devices to determine functionality. Simulate overpressure conditions to ascertain that relief valves and sensors respond correctly.
By doing these things, it will enable the pressure control devices to function well hence keeping the right range of pressure for rotary lobe pumps. Regular monitoring and maintenance increase the pump’s efficiency as well as its lifespan thereby preventing potential failure points and expensive repairs.
Seal Maintenance
Types of Seals
Common Seal Materials
Rotary lobe pumps rely on seals in order to keep up with the pressure required while ensuring zero leakage in operation. Common materials for these seals include:
- Elastomers: Elasticity coupled with resistance against wearing out marks elastomers as a popular choice among many industries.
- PTFE (Polytetrafluoroethylene): Fantastic chemical resistance plus low friction makes PTFE widely accepted within different applications where such qualities are necessary.
- Ceramics: They have good durability characteristics besides being able to withstand high temperatures without getting damaged easily.
One must choose the most suitable material depending on application specifics as well as pumped fluid properties.
Choosing the Right Seal
Selecting the appropriate seal involves several considerations:
- Fluid Compatibility: Make sure that seal materials are compatible with fluids being handled during pumping processes.
- Operating Conditions: Take into account temperature levels, pressure ratings and speed limits required by various working environments alongside this equipment type used in them respectively.
- Design Features: Go for those designs which match specifications described by manufacturers while considering operational requirements set forth herein before such selection is made too hastily or based purely upon personal preference alone without enough background knowledge concerning what works best where under given circumstances may arise from time-to-time among unsuspecting users who never bother about such matters until something goes wrong eventually leading towards unnecessary costs being incurred due negligence on their part.
Alternatively, high-performance seals like Springer Parts’ often exceed OEM standards and therefore they are more reliable and last longer.
Seal Replacement
Steps to Replace Seals
- Preparation: Have all necessary tools ready along with replacement seals.
- Shutdown: Switch off power supply then disconnect it from its source before anything else is done here.
- Disassembly: Take off front cover so that access can be gained into seal area where work needs to be done next.
- Removal: Remove old ones carefully without causing any damage around them or nearby components which might also require attention later on in this process if not taken care properly at initial stages already mentioned above.
- Cleaning: Clean the housing for these parts as well as those regions surrounding them for proper hygiene purposes before moving onto installation stage itself which comes right after step four below;
- Installation: Put new ones back ensuring alignment is correct throughout before tightening everything up securely thereby ensuring leak-free operation afterwards during subsequent usage periods over time;
- Reassembly: Put back together everything which was taken apart during disassembly phase while ensuring that each item finds its rightful place within the overall structure of things here involved hence allowing smooth flow throughout entire system concerned thus making sure no further dismantling will have to take place except when absolutely necessary eg; for maintenance reasons or due some mechanical faults arising from wear tear etc..
- Testing: Run machinery checks involving pumps themselves by running them under load conditions following successful completion of repair works carried out earlier mentioned steps up to this point only then can we say that our job has been completed successfully according to instructions given at beginning part.
Maintenance Procedures
Drive Systems Lubrication
In both belt and gear drive systems, proper lubrication is a must. Lubricants lower friction and prevent wearing out. Synthetic oils have better performance and can be used for longer periods than other types of lubricants. Always follow the manufacturer’s instructions on what types of lubes to use and the best application times. Regularly check how oily it is or fill it up if necessary. Good lubrication leads to smooth-running machines.
Wear and Tear Checks
Frequent checks should be made for signs of wear and tear in any system that relies on moving parts. For belts, look out for frayed edges, cracks across their width or lengthways stretching beyond what they were designed for etc.. If these are seen then replace them immediately as slip could occur which would lead onto other faults occurring such as burning out motors etc.. Similarly with gears check each tooth carefully looking particularly at where power is transferred through meshing together while rotating around its axis but also where forces are applied from outside during operation causing rubbing against other teeth – if any chips or elongated shapes due to abrasion are found here then again replace straight away so that transmission always remains smooth between shafts involved!. Use suitable instruments/measuring equipment when determining amount worn away i.e micrometers if metal on metal contact etc.. Finding out early what’s starting off small prevents bigger problems later on becoming more expensive fixes too maintain..
Drive systems maintenance includes procedures aimed at ensuring reliable functioning and efficiency of rotary lobe pumps. The life span of equipment is extended through regular greasing and check-up ups. When dealing with belt-and-gear mechanisms one should take care of them well because they contribute greatly into overall pump performance.
Records and Documentation
Reasons for Documenting
Tracking Work Done
All activities carried ought to be properly recorded without exception. This enables technicians to identify recurring issues by referring back to previous cases encountered within machines. Also, it helps them know when the next service is due among other things. Having accurate records ensures that no essential task is left out.
Benefits of Recording in Detail
There are numerous advantages to detailed record keeping. For example; it provides an account of how the rotary lobe pump has been performing over time which Technicians can rely on while trying to solve problems. Accessing past data assist in faster diagnosis by these experts since they already have some background information concerning a particular equipment/component failure mode etc.. Compliance with industry standards becomes easy with comprehensive documentation such as this one here. Properly maintained records can even boost their resale value especially if they show regular maintenance which indicates care taken over the years..