Selecting the right kind of pump for industrial purposes is critical for performance and reliability. Among the numerous widely used positive displacement pumps are gear and lobe pumps, and these have their distinctive features as well. This article hopes to provide an extensive comparison so that suitable and informed choices are made.
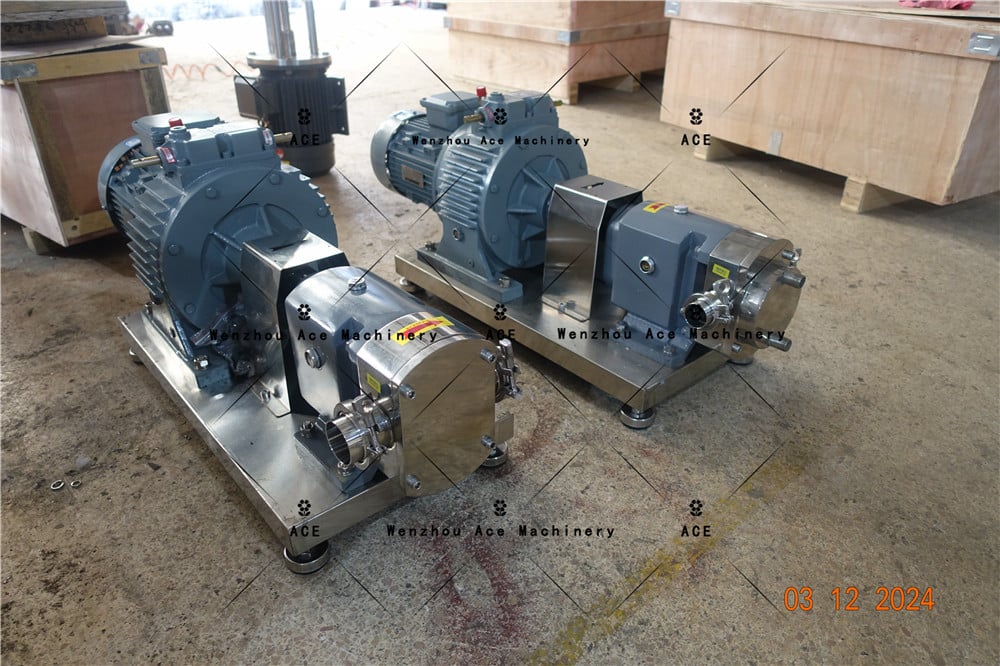
Explaining Gear Pumps
Under gear pumps, there are two or more rotating gears that mesh together to create a cavity, thus pump out the liquid to the destination. They are categorized into:
External Gear Pumps
These incorporate two identical rotating gears that mesh externally.
Internal Gear Pumps
These have an outer gear which is wider than the drive gear and is equipped with a bench cut to enhance spacing.
Gears, pH, hermetic pumps, lobe pumps, and graphite lobe pumps work under the same fundamental principles.
Advantages of Gear Pumps
- Design: Their construction makes maintenance considerably easy.
- Pressure Levels: Able to operate to higher levels, making it be used in various industries.
- Price: Because of easy design, generally cheaper.
Disadvantages of Gear Pumps
- Limited Lifespan: Wear occurs due to continuous meshing of the cogs until lubrication occurs.
- High Vibrations & Sound: Due to the greater noise created by the pump compared to other types, it is usually accompanied by higher vibrations.
- Poor Performance: In addition to using high viscosity fluids, sensitive shear fluids are also less effective.
Understanding Lobe Pumps
Lobe pumps can also be referred to as rotary lobe pumps. These lobe pumps operate using lobes that rotate to transport fluid. Because the lobes do not touch each other, a lobe pump prevents the fluid from significant damage.
Advantages of Lobe Pumps
- They can pump fluids that are sensitive to shear force, which makes them ideal for industrial applications where such forces must be controlled.
- They can manage a variety of viscosities as well as solids. Because of this, it is suitable for use in the food processing and pharmaceutical industries.
- They are simple to clean and maintain while complying with high sanitary requirements.
Disadvantages of Lobe Pumps
- One of the major downsides of rotating lobe pumps is that they consist of a more complex design in comparison to gear pumps. Therefore, they tend to be more expensive.
- Additionally, they tend to have low pressure limits.
Application Suitability
In terms of fluid handling, lobe pumps are able to handle high-viscosity fluids, whereas gear pumps are able to handle low to medium viscosity hydrocarbon fluids.
Maintaining structural integrity is crucial for some fluids as they are easily damaged. Lobe pumps eliminate wear and tear on these fluids, which in turn makes them desirable for several industrial applications.
Gear pumps: Utilized in applications with high pressure and precision flow control.
Lobe pumps: Used in industries that require less pressure and higher standard of hygiene.
Selecting the Appropriate Pump for Your Application
When it comes to the selection of gear or lobe pumps, the following factors must be noted:
- Fluid Characteristics: Viscosity, sensitivity to shear, and solids content.
- Operational Conditions: Required pressure and flow rate, temperature, etc.
- Maintenance Considerations: Complexity in cleaning and frequency of maintenance repairs.
- Cost Implications: Start up costs as opposed to operational expenditures over the long-term.
Conclusion
Lobe pumps and gear pumps have their benefits and limitations. It is important to have an understanding of differences which exist if the correct pump is to be selected for particular industrial requirements.
Frequently Asked Questions
Are there major differences between lobe pumps and gear pumps?
In gear pumps, flow of fluid is achieved by rotating two gears that are in contact, causing meshing the fluid. These pumps are used for low to medium viscosity fluids. Fluid to be pumped is enclosed in chambers IP and OPS where non-contacting lobes tip the difference, and these are best suited for shear sensitive fluid with high viscosity.
Are lobe pumps suitable for high pressure applications?
From a broad perspective, gear pumps are used for higher pressure applications more frequently because of their general design.
Does the cost of lobe pumps surpass that of gear pumps?
First off, lobe pumps, which have advanced engineering and construction, would incur an increased cost at first. However, gear pumps can offset the maintenance and lifespan expenditure.
How about dealing with gear pumps and solids in a fluid?
As for a combination of fluids with solids, gear pumps may be deemed as not very effective, as the solids may wear and damage.
Which of the pumps is less hassle to keep?
Generally, lobe pumps are easier to maintain because of their non-contacting mechanism and ease of cleaning.
What industries utilize lobe pumps the most?
Lobe pumps are increased in the food industry, pharmaceutical industry, and biotechnology because they are less aggressive in operation and are more hygienic.
Final Information
You may check this comprehensive analysis to compare between lobe pumps and gear pumps. Comparison Overview Guidelines: Comparing between Gear Pumps & Lobe Pumps: Giving You Insights on What to Consider.