A Guide To High and Low Shear Mixers, What Are The Differences and Which One Should You Choose
Selecting the right type of mixer for a specific application is one of the high priority choices that must be made. The application of a certain type of mixing technology can greatly enhance one’s productivity along with qualitative output. In a multitude of sectors, high shear and low shear mixers are some of the most frequently used categories of mixers. This blog will assist you in making your decision by providing a thorough explanation of the applications, advantages, factors, and most importantly the differences between both the shear mixers.
High Shear Mixer Definition
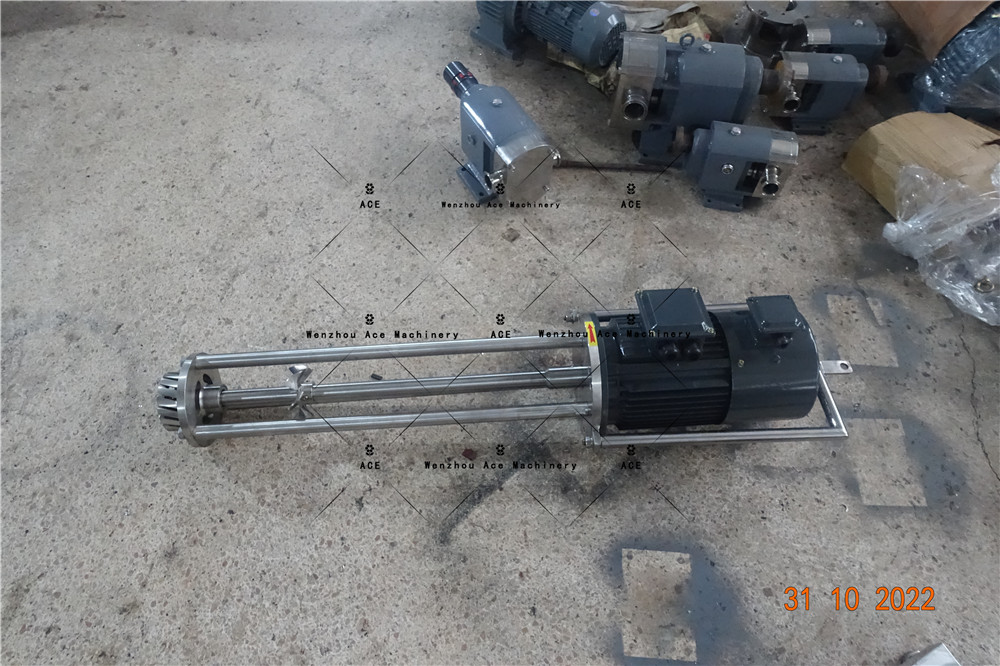
Mechanism and Definition
High shear mixers are recent and improved mixing devices that utilize intense shear forces to force mixing of a material or several materials in a very short time. The rotor and stator assembly is the most common high shear mixer configuration. In this configuration, the rotor spins at high speeds in a stationary stator. This aids in generating a vortex where the materials get high flow rates. The high shear forces produced in the process ensure extensive particle breakdown during dispersion, emulsification, and homogenization.
Applications
High shear mixers are widely used in:
- Manufacturing of pharmaceutical products
- Production of beverages and food
- Creation of cosmetics and personal care products
- Processing of chemicals
- Usage in paints and coatings
Advantages
- Fast Mixing of High Shear: High shear mixers have short mixing times compared to low shear mixers, improving efficiency in productivity.
- Mixing and Homogenization: These mixers have high effectiveness in mixing and homogenizing processes of materials.
- Wide Range Mixers: Able to accommodate different viscosities and materials.
- Quality Assurance: Guarantees uniformity of the end product, which ensure minimal differences in the products of different batches.
What is a Low Shear Mixer?
Definition and Mechanism
As the name suggests, Low shear mixers have an application for products that require a softer approach. They function at lower rotational speeds and develop a lower amount of shear force, thus can incorporate sensitive materials without damaging or changing their structure. Paddle mixers, ribbon blenders, and planetary mixers are the most typical low shear blender types.
Applications
Low shear mixers are highly recommended for use in:
- Computer aided plastic assembly
- Agricultural industry
- Food processing that uses low shear
- Pharmaceutical products that are soft in shear processing
- Make up products that use food as an ingredient
Advantages
- Soothing Mixing: Appropriate for use where the product requires no adverse effects to them.
- Cut down energy expenditure: Use less energy.
- Material Properties Preservation: Avoids damage to delicate elements.
Low Shear Mixer and High Shear Mixer: Core Differences/Characteristics
Mixing Speed and Efficiency
Very high mixing speed and shear means a high-speed volume-homogenizing machine is a high-shear mixer, and so, it blends materials quickly, thus cutting down mixing time, and effectively disperses any particulate matter use with the mixing process. Low shear mixers, however, use a slower speed since they deal with mixing and need to ensure the components mixed few damaged while doing so.
Particle Size Reduction
High shear mixers are effective in reducing agglomerates and particle sizes due to the combination of high shear and speeds which results in finer and more uniform mixtures, in contrary low shear mixers are not ideal for this process due to the fact they can’t do this or homogenization well at all.
Application Suitability
Mixers that work with tough particles as well as high viscosity materials require emulsification, homogenization and dispersing, which high shear mixers do best at. Delicate and sensitive components/machines which cannot be mixed with high shear and still remain intact are best mixed using a low shear mixer.
Maintenance and Expenses
High shear mixers function optimally in selected tasks, but they are pricier and need expensive structural components which require more maintenance too. Contrastingly, Low shear mixers are more cost-effective while needing lower maintenance too.
Considerations that Influence the Choice Between A Low Shear And A High Shear Mixer
There are several considerations that influence the choice of a mixer:
- Nature of Materials: Evaluate if the materials you are dealing with are shear sensitive or require thorough dispersion.
- Desired Outcome: Establish whether the objective is total homogenization, reduction in particle size, achieving a well disbursed mix or gentle homogenization.
- Production Scale: What is the size of your production? High shear mixers are generally more effective in larger, high volumetric production processes.
- Cost and Budget: Determine your cost of procurement and running the mixer and see if it meets the needed aim.
- Regulatory Requirements: Some regulatory bodies of specific industries, e.g. the food and pharma industries, may impose strict constraints which would limit the kind of mixer incapacitarian.
Frequently Asked Questions about High Shear and Low Shear Mixers
What meat kinds are best to combine using a high shear mixer?
A high shear mixer performs well on meat amalgamation related to emulsification, homogenization, and more. As an example, there are some food products, cosmetics, and pharmaceuticals that would best fit this category.
Do low shear mixers work on highly viscous items?
Low shear mixers can mix high viscous materials but would not dethrone a high shear mixer when it comes to viscosity. They work well in gentle blending processes.
Do high shear mixers use a lot of energy?
A high shear mixer requires a lot of energy to efficiently function due to their high speed of use, however the uniformity of the product tends to justify the increased cost as it cuts down on lengthy mixing issues.
How do high shear mixers provide uniformity?
The blend of particles within the mixers are often broken down and dispersed using a high force to maintain the end products a blend of high quality and lesser changes batch to batch.
Can I replace all other mixers with a high shear mixer for my mixing requirements?
High shear mixers are good for a set of applications but not all, the ones that include high sensitive components for example do not fall under that category. It is recommended to first check requirements before high shear mixing.
Conclusion
When selecting a high shear mixer or a low shear mixer, you have to consider how each likely differs and what requirements you have, while also keeping your production goals in mind. If a mixer is wrongly chosen, product quality and production outcomes are likely to suffer, so ensure you choose the right one.